ABOUT US
For the past fifty years, our company has been a well-known protagonist of the sector of machines for working profile sections for frames.
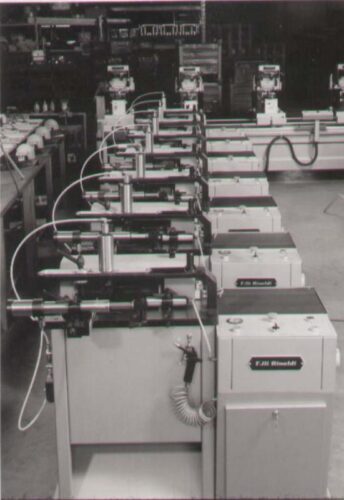
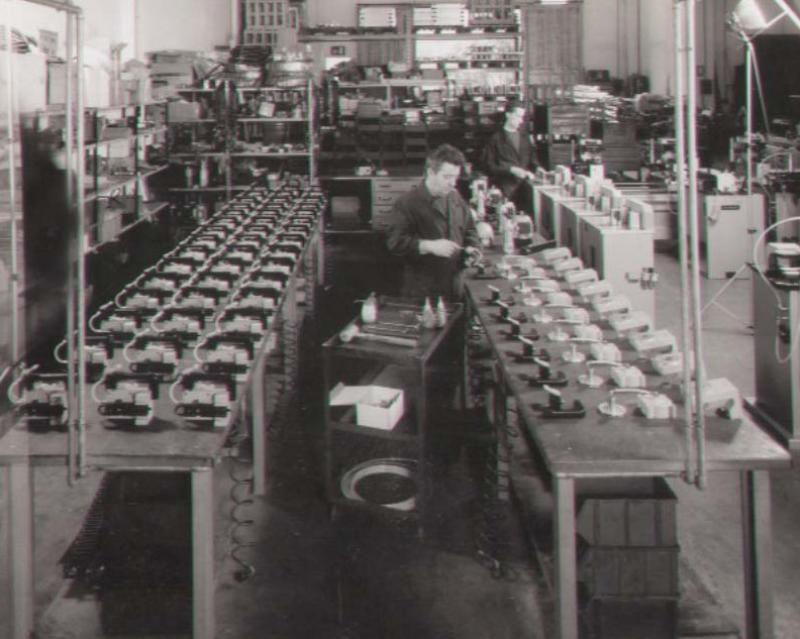
HISTORY
In the Eighties, the company grew thanks to ongoing technological developments and diversification of models; business partnerships with major companies in the industry have made our products known worldwide.
Our strong point, including thanks to the endeavours of distributors and dealers, remains the professional experience acquired through contacts with thousands of end customers.
Today, the company is run by the second generation, headed by Massimo Rinaldi, along with Franco, Luciano and internal and external staff members who, through design, production, sales and assistance, contribute to the success of our products; production Vignola (Modena) Italy.
MISSION
Because we have the satisfaction of our customers at heart, we provide them with innovative, efficient products and prompt service; all this by investing in research, training and ongoing product upgrading; exploiting the latest available technologies, including from other sectors.

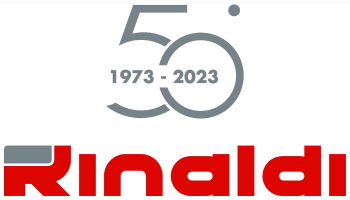
TECHNOLOGY
Over the years, we have launched numerous innovations in the industry, including thanks to the contribution of distributors, dealers and end customers; among the major ones are:
Punching machines
> the Seventies – first pneumatic portable punching machine weighing only 4.5 kg.
End milling machines
> > the Eighties – introduction of the manual and then pneumatic cutter unit quick change; speeds up all positioning operations.
> > the Nineties – presentation of soundproofed version; thanks to a tunnel which encloses the profile section, sound emissions are reduced to around 75db.
> > 2000+ - fitting of electronic speed variator to regulate the spindle rotation speed; the increase in speed improves machining quality.
> > 2010+ – launch of fully-automatic version, including guard and tunnel cover opening and closing.
Copy routers
> > the Nineties – introduction of height stroke recovery; by means of a lever the work height of the Z axis can be increased by 50 mm to machine high profile sections.
> > the Nineties – introduction of the DISC template; speeds up positioning operations returning each figure to the worktop centre.
Copy routers for iron
> > the Nineties – These models were designed to carry out typical aluminium machining operations on steel profile sections.
> > 2000+ - introduction of the rotating clamp plane which permits machining 4 sides of the profile section without releasing the clamps; this speeds up operations on several sides of the piece. Featuring a system which, by rotating from 0° to 180° maintains the same work axis.
> > 2010+ - The air cooling system at -10°C together with an impulse lubricator with neat oil permits extending tool life when working stainless steel.
Cut-off machines
> Year 2010 - the company understands the importance that aluminium is having in the industrial sector as well, so it builds ascending cutting-off machines to cut profiles not only for window frames but also thick industrial profiles. In the years to come, improvements have been applied, such as pneumatic blade change, the possibility of applying different blade diameter sizes and consequently the application of inverters to improve cutting quality.
> Year 2012 - Rinaldi implements the variety of its products by starting to produce the double-head cutting-off machine.
Machining centres
> Year 2013 - production starts on the 4AX machining centre with electrospindle and tool changer
> Year 2021 - the market is changing fast, as shown by the many requests for 5AX machining centres, especially in the industrial sector, so that by the end of the year Rinaldi will present a very innovative 5AX machining centre both as a standalone centre and as a centre with automatic loading and unloading.